ABOUT US
New Zealand Owned and Operated
OUR STORY
Dedicated to innovation and making the best cement and cement substitute products in New Zealand, both sustainable and high-performing.
Our goal is simple; to make better products that are easy on the planet without compromising on the quality.
We recognised that the industry needed to reduce its carbon footprint, and after years of testing and innovation, we are the first in New Zealand to make and supply a BFS-based cement replacement material and so enable production of truly low carbon concrete.
Certified Processing
HR Cement is ISO9001 certified for the entire production process.
We have an on-site laboratory for initial quality testing and then our products are further independently tested to ensure we conform with the NZ Cement standard NZS 3122:2009. The results are published weekly.
We have EPD's for Xtra-Cem GP Cement and Eco-Cem, an independently verified assessment of the impact of our products.
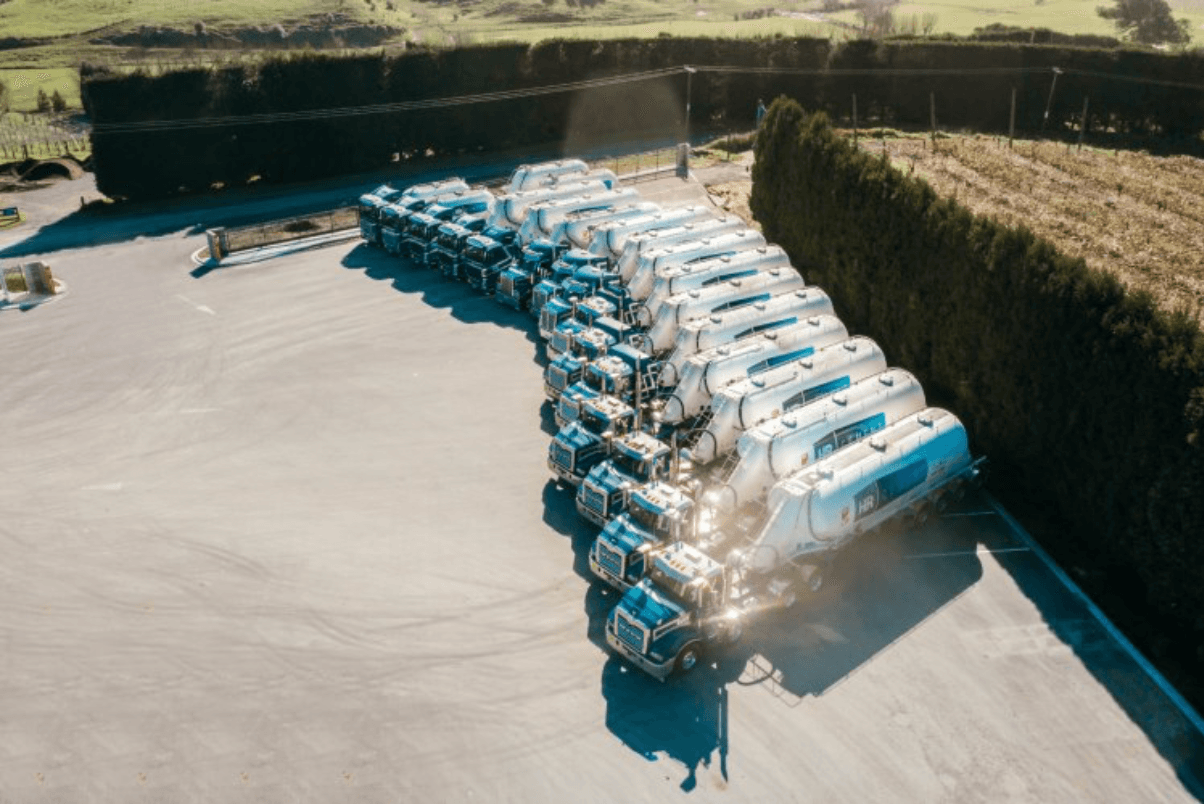
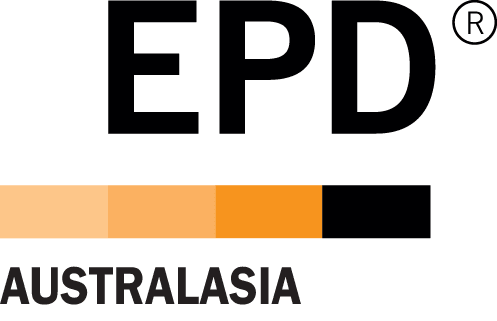
Our Pursuit of the
Industry-defining SCM
Supplementary cementitious materials (SCMs) are a class of minerals that can be used to substitute cement. The Romans understood the earliest SCM (a natural volcanic pozzolan) well, mixing this material with burnt lime to create the early cement used for the Pantheon and the Pont du Gard which still stand today.
During the 1950s in New Zealand, natural pozzolans (pumice) from the Central Plateau were used in concrete to build the Waikato dams and other associated projects. This followed extensive DSIR trials, and the Ātiamuri, Waipapa and Ohakuri projects are testament to their longevity.
Our Product Development Journey
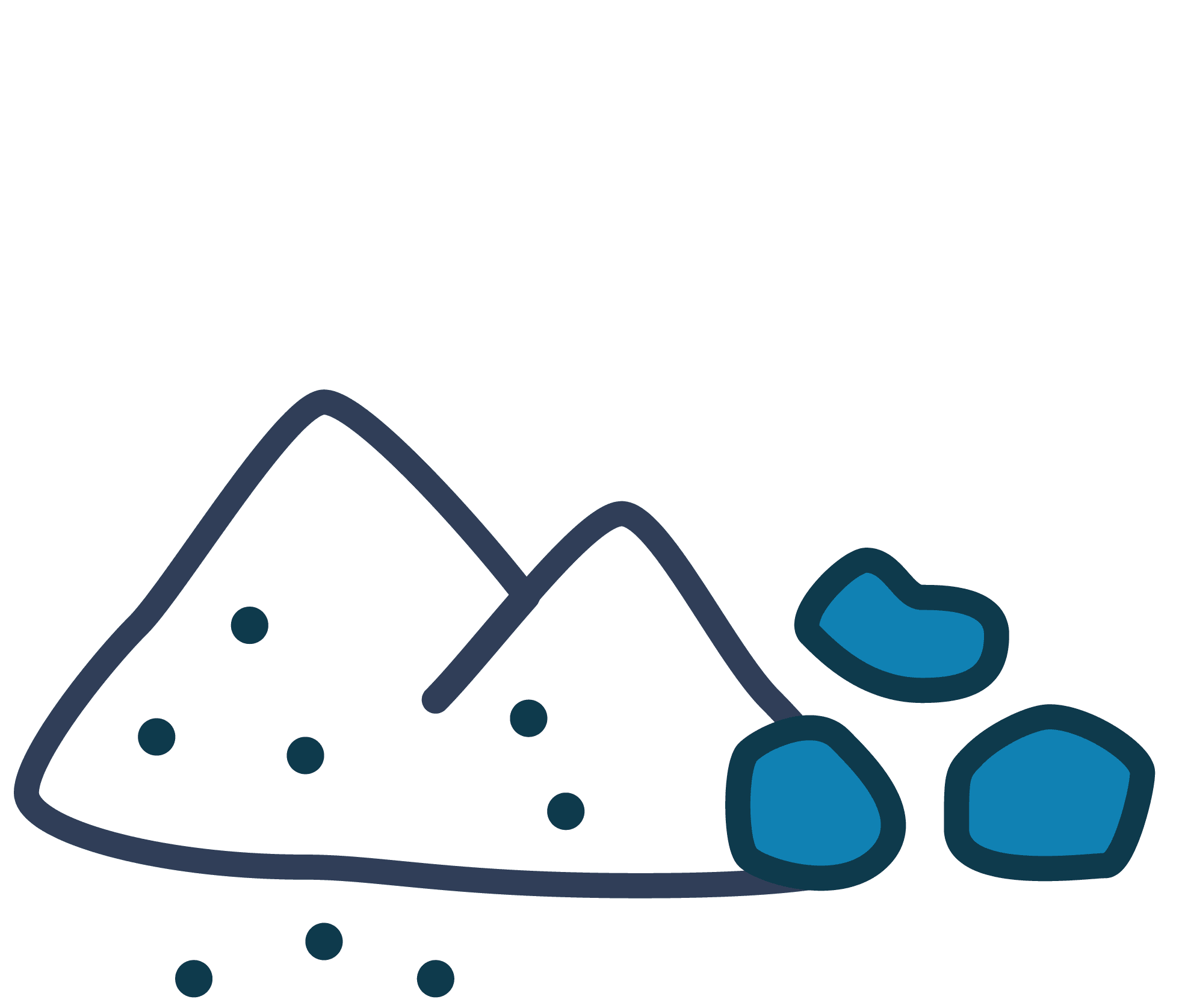
We originally investigated a blended cement, and the journey began with testing natural pozzolans as a potential base of our carbon conscious cement.
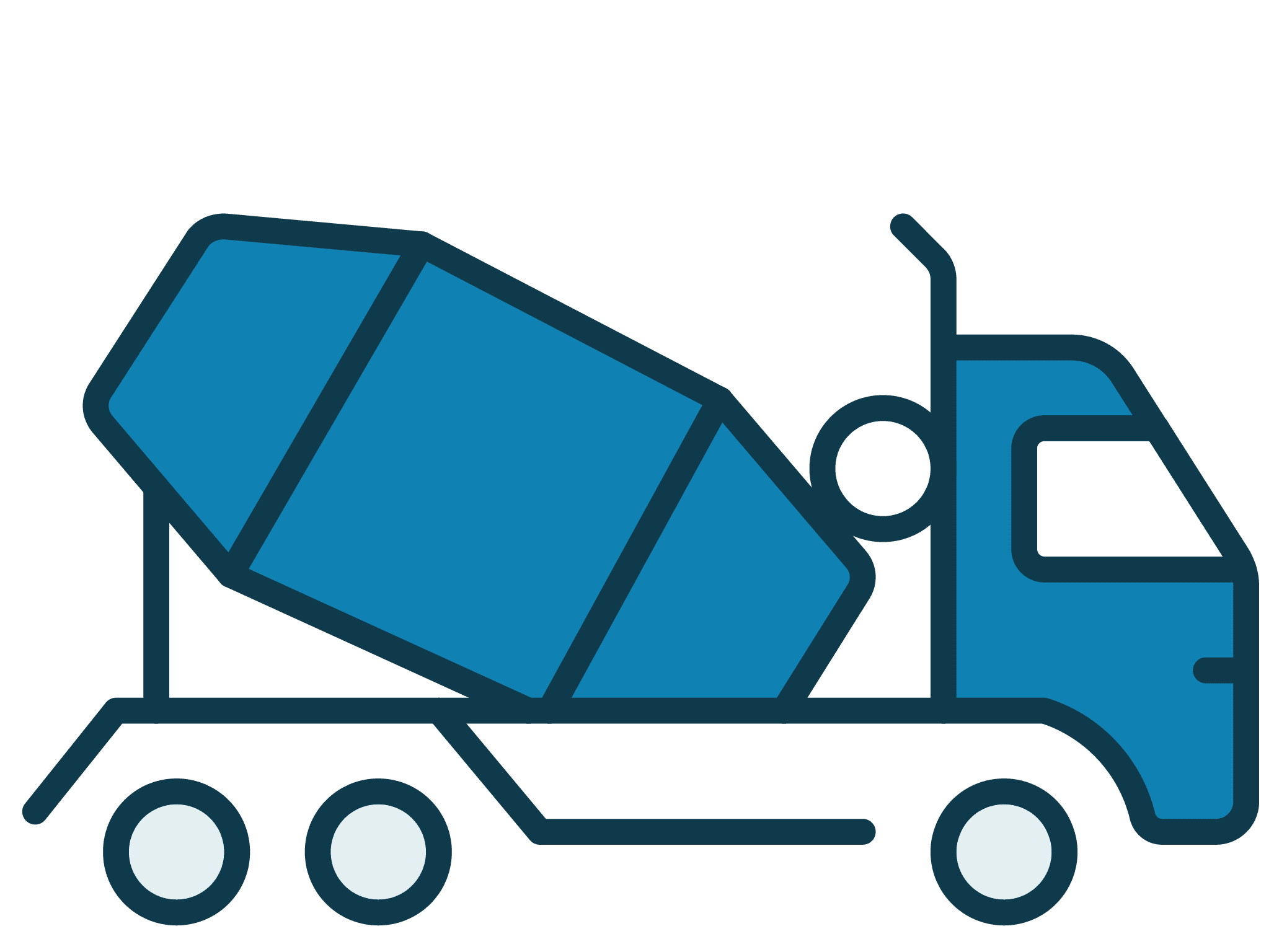
This investigation involved Callaghan Innovation, overseas labs, small-scale trials, and pilot production. With a successful blended cement concept and tonnes produced, HR Cement received a Technology Award Commendation from the NZ Concrete Society in 2017.
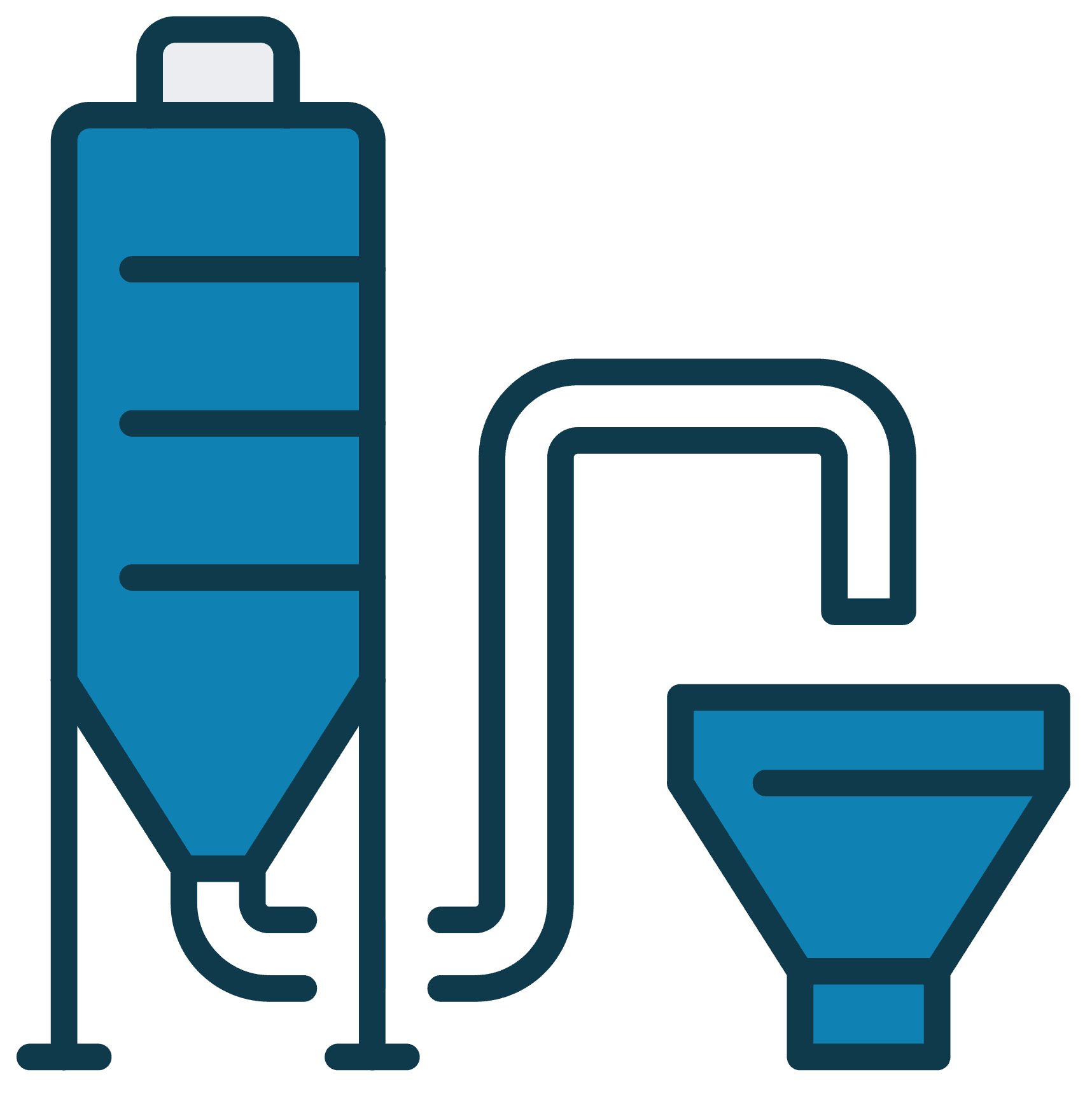
This work continued until 2018, when it was concluded that while viable, natural pozzolans face commercial challenges due to their low reactivity. More efficient solutions exist, that said, we feel natural pozzolans will probably feature in the future as the market evolves.
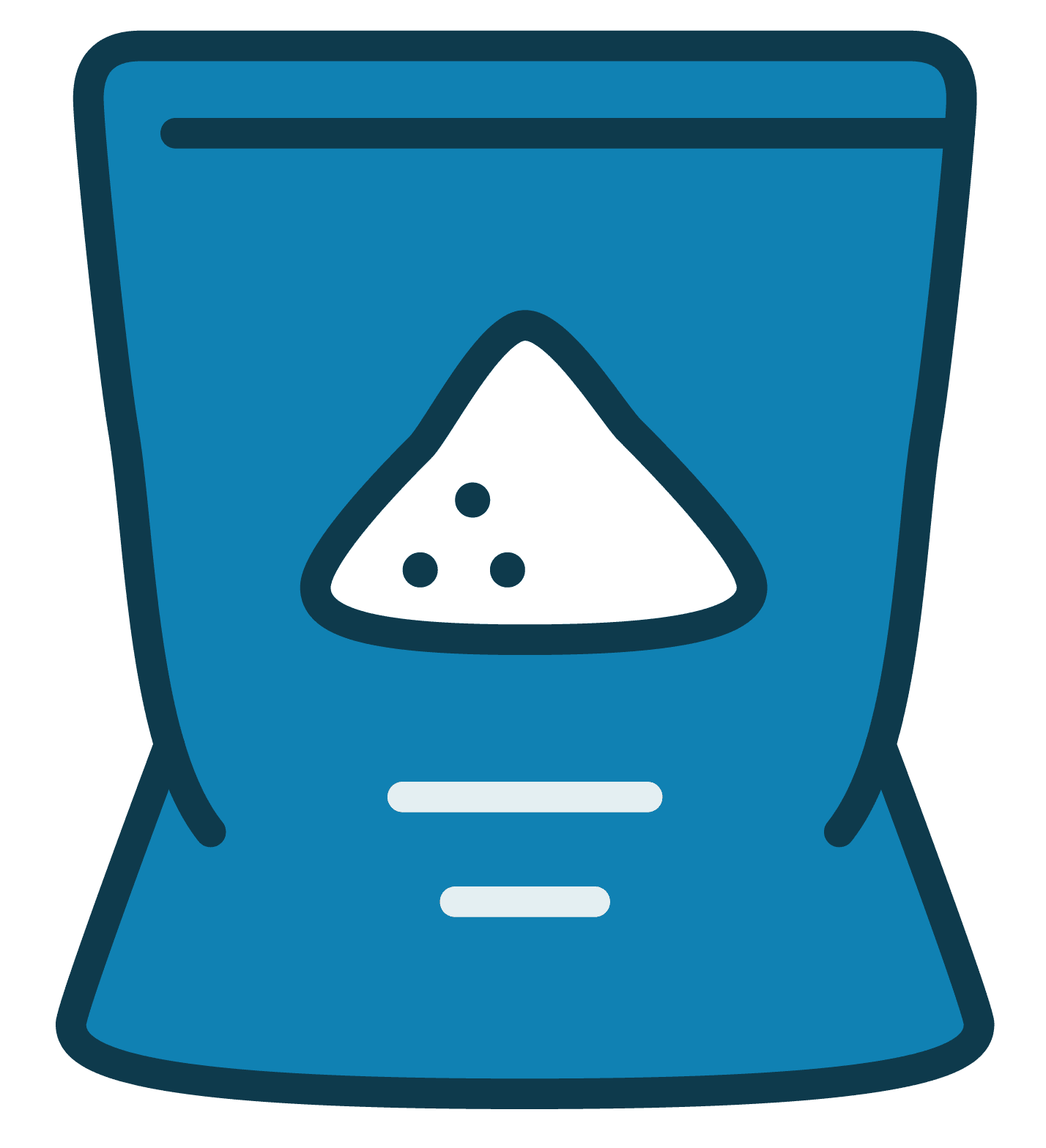
Our research into Blast Furnace Slag (BFS), a by-product of steel production, created a more efficient product while still meeting our low carbon goals.